In today’s fast-changing eyewear world, sustainability is key. THY Precision leads in injection moulding process step by step solutions. They’re making eyewear production more eco-friendly. Imagine, the future of THY Precision Injection Molding Optical Lenses is close by. Let’s explore how new practices are changing plastic molding and molding techniques.
Key Takeaways
- Discover how THY Precision is leading the charge in sustainable injection moulding process step by step for optical lenses.
- Explore the latest eco-friendly molding process phases and molten plastic injection techniques that are revolutionizing the industry.
- Learn how the shift towards sustainable plastic product manufacturing is shaping the future of eyewear.
- Understand the importance of mold cavity filling and cooling and ejection stages in achieving optimal sustainability.
- Gain insight into the practical steps you can take to incorporate sustainable practices into your own Injection Molding Optical Lenses operations.
The Importance of Sustainable Injection Molding Optical Lenses
In today’s world, we’re all thinking more about being eco-friendly. The injection moulding process step by step is no exception. It’s used to make many things, from car parts to toys. But, it can also harm the environment. Yet, by going green, the plastic molding industry can cut down on waste and costs. This makes it better for our planet.
The way we do molding techniques in molten plastic injection is key to being green. By making the mold cavity filling and cooling and ejection stages better, we can use less energy and waste less material. This makes our products better for the earth.
- Using green practices in injection moulding cuts down on energy use and emissions. It also makes our environmental impact smaller.
- Choosing recycled and bio-based materials in Injection Molding Optical Lenses helps us use less new plastic. This supports a circular economy.
- Improving molding techniques and molding process phases makes the molten plastic injection process more efficient. This means less waste and cheaper plastic product manufacturing.
“Sustainable Injection Molding Optical Lenses is not just about being eco-friendly – it’s also a smart business strategy that can lead to cost savings and improved competitiveness in the market.”
By choosing sustainable ways in injection moulding, companies can lessen their environmental harm. They can also boost their profits and stay ahead in a market that cares more about being green.
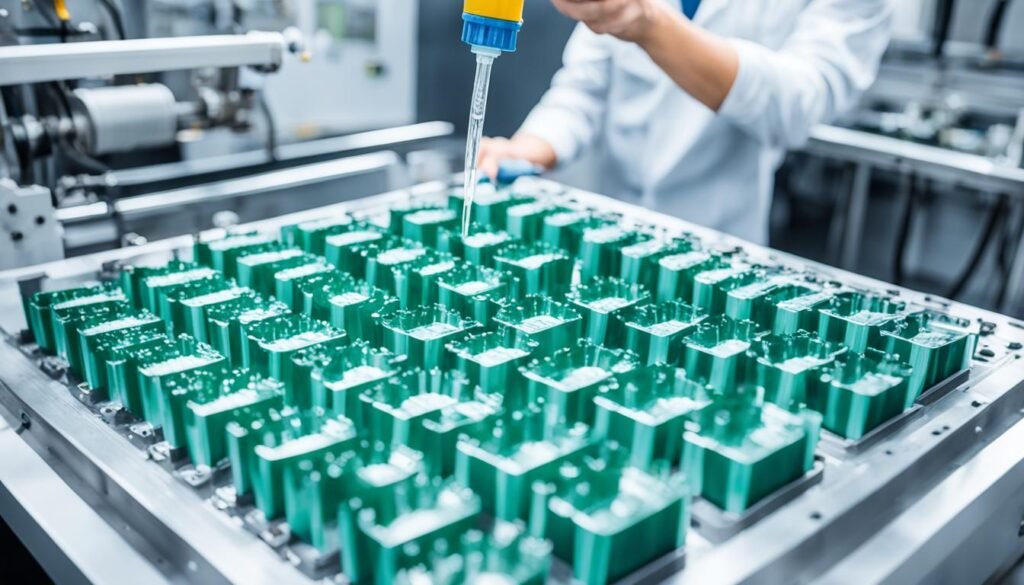
Injection Molding Optical Lenses – Utilizing Recycled and Bio-Based Materials
The injection molding industry is finding new ways to be more eco-friendly. They’re using recycled plastics and materials from nature in the injection molding process.
Recycled Plastics in Injection Molding Optical Lenses
Now, recycled plastics are a good choice for injection molding. They can go back into the molding process. This is thanks to closed-loop recycling, which turns recycled plastics into high-quality products.
Using recycled plastic helps reduce the need for new plastics. It also means using less fossil fuel and less plastic ends up in landfills.
Bio-Based and Biodegradable Polymers
The plastics industry is making greener options because of the big environmental impact of traditional plastic. They’re creating bio-based plastics, biodegradable plastics, and compostable plastics. These can be used in plastic injection molding.
Choosing these sustainable plastics lowers the carbon footprint and reduces plastic waste. It shows the industry’s effort to be more eco-friendly.
By using recycled plastics and new materials from nature, the injection molding industry is moving towards a greener future. These choices help our planet and show the industry’s dedication to making plastic products responsibly.
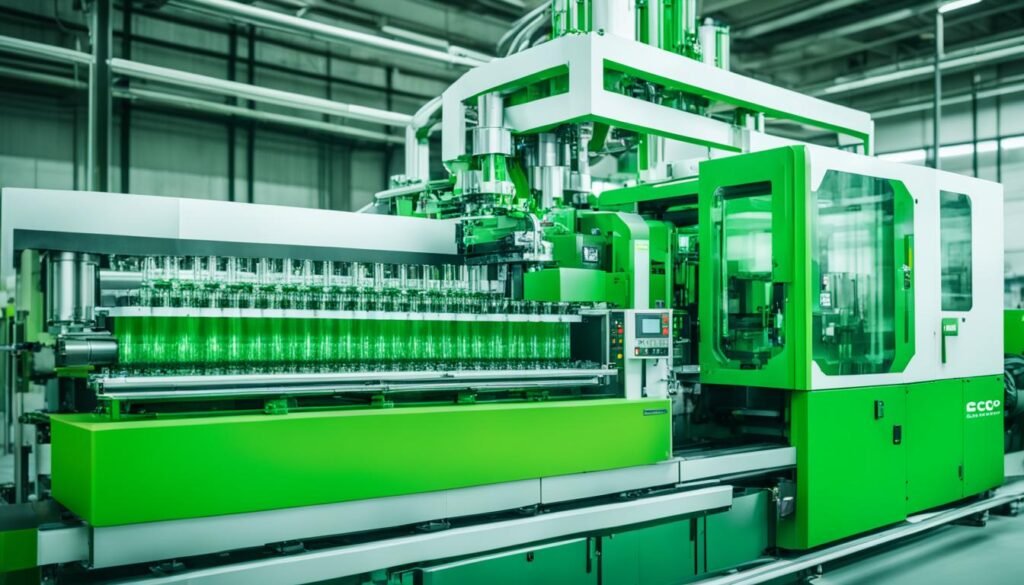
Injection Molding Optical Lenses – Energy Efficiency and Renewable Resources
At THY Precision, we know how vital energy efficiency and sustainability are in the injection moulding process step by step. The plastic injection molding industry is changing. Now, new plastic molding methods and molding techniques make the process more energy-efficient.
Using energy-efficient electric plastic product manufacturing machines is a big step forward. These machines use less energy when filling the mold cavity and cooling. They also help us control the process better, making us more efficient and using less energy.
THY Precision also uses renewable energy to make our injection molding even greener. This choice cuts down our carbon footprint. It helps make the plastic molding industry more eco-friendly.
Energy Efficiency Measure | Impact on Injection Molding |
---|---|
Energy-efficient electric machines | Reduced energy consumption during the injection moulding process step by step |
Tighter process parameter control | Increased production efficiency and reduced energy waste |
Renewable energy sources | Decreased carbon footprint and enhanced sustainability |
At THY Precision, we aim to make the injection molding industry more sustainable. By using energy-efficient tech and renewable energy, we’re leading the way to a greener plastic product manufacturing future.
“Sustainable practices in injection molding not only benefit the environment, but they also contribute to the long-term success and competitiveness of our business.” – THY Precision CEO
injection moulding process step by step: Optimizing Operations
At THY Precision, we know the injection moulding process step by step is key for making top-quality plastic items. We go beyond the basic steps like injecting molten plastic, filling the mold, cooling, and ejecting the product. Our team works hard to make our operations better, cutting down on waste and working more efficiently.
We focus a lot on waste reduction. The extra material, or sprues, from the injection molding process is often thrown away. But at THY Precision, we don’t waste it. We use our own machines to turn this plastic into something useful again. This helps the environment and makes our plastic molding process smoother, saving time and resources.
Also, we follow lean manufacturing to make our operations better. This means we cut down on wait times and costs, while making more products and keeping quality high. By doing this, we offer our clients plastic product manufacturing solutions that save money and are good for the planet.
Molding Technique | Waste Reduction Strategies | Lean Manufacturing Initiatives |
---|---|---|
Injection Molding |
|
|
At THY Precision, we aim to lead in molding techniques and molding process phases. We want to offer top-notch plastic product manufacturing solutions that are good for the planet and save money. By always improving our injection moulding process step by step, we aim to set new standards in plastic molding.
“At THY Precision, we are committed to driving innovation in the injection moulding process step by step to deliver exceptional plastic products that are both environmentally responsible and economically viable.”
Conclusion
When you look into plastic product manufacturing, choosing sustainable injection moulding is key. Working with THY Precision, a top name in eco-friendly injection molding, puts you at the forefront of sustainability.
THY Precision shows their dedication to sustainability through strong environmental management and ongoing improvement. By using their knowledge, you can boost your brand’s green image. This will draw in customers who care about the planet.
Going for sustainable injection moulding helps the environment and secures your business’s future. It keeps you ahead in the market by meeting the growing need for green products. Start with sustainable injection moulding and lead the way in the industry’s shift towards green practices.